When we see customers saving millions after replacing wood and plastic pallets with paperboard slip sheets, we wonder why more companies aren’t doing the same.
One deterrent we often hear about is that the initial research seems like it will be painful, but that does not need to be the case. Our packaging engineers follow a process so you can more easily consider the benefits and requirements of slip sheets (sometimes called push pull sheets).
Start with the basics.
- Load size: The footprint of the product–usually corrugated cartons–such as 40×48. The bottom area of the stacked product has what width and length?
- Load weight: The total weight of the products placed on the pallet–soon to be paperboard slip sheet. One full pallet of product weighs how much?
- Stacking requirements: The number of pallets which plan to be moved at one time. Will loaders or unloaders want/need to move a stack of two pallets at the same time?
- Handling conditions: The environment. Is this pallet of product ever in damp conditions? Is the load pretty stable or many layers of small boxes and unstable?
These factors guide the packaging engineer in determining the range of options available. The size, weight and stacking requirements inform the minimum paper strength needed to safely and consistently move the product. The handling conditions inform the potential need for coatings–moisture resistance or non-slip–and any factors suggesting you may need to upgrade strength.
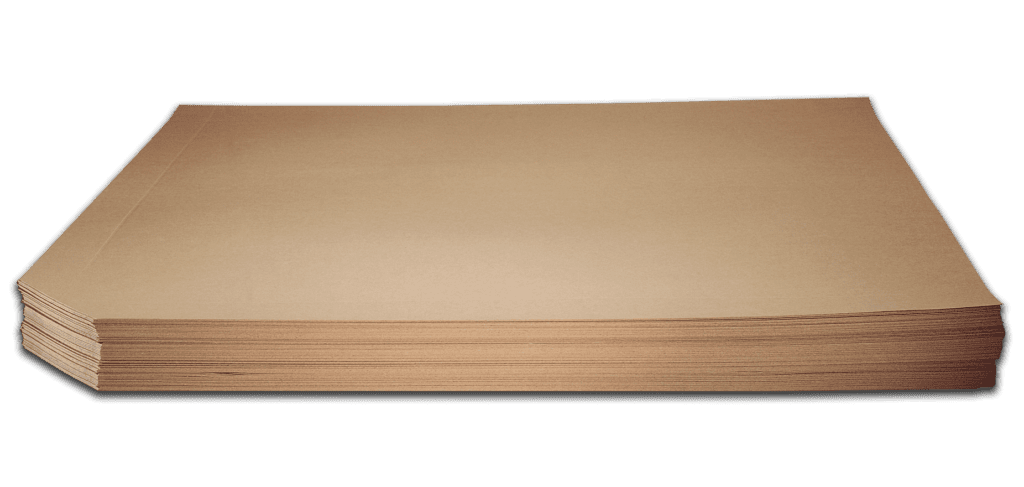
Calculate expected load stress for the slip sheet.
Load stress data is used to determine the expected working stress of the load. The key test used on the papers is tensile strength–a measurement of the material’s resistance to being pulled apart. Standardized testing methods such as TAPPI T 494 and ASTM D828 are conducted on specialized testing machines. The force required to break the sample is recorded, and the tensile strength is calculated. Several factors influence the tensile strength of paperboard slip sheets: fiber type–virgin or recycled; thickness; moisture content; and additives and coatings. We do the heavy lifting for our customers to answer for these variables.
Choose a safety factor.
Safety factor is a ratio that compares the strength of a material to the actual load it will experience. The general safety factor range is 1.5 to 3.0. A 1.5 safety factor means the slip sheet is designed to withstand at least one and a half times the expected load–which might be chosen for low-risk applications. A low-risk example might be internal company transfers of light loads of light product that aren’t too difficult to hand stack on the rare occasion of failure. A safety factor of 3.0 might be chosen for high-risk–say heavy loads of heavy product moved in and out of freezer storage and unloaded by pulling two stacks at a time out of the truck. You don’t want this one to ever fail, so you add more safety.
Of course, it is crucial to conduct thorough testing of the slip sheet under actual operating conditions. Trials of several strengths and resulting safety factors are often best for comparison and can be integrated into the process depending on your use case.
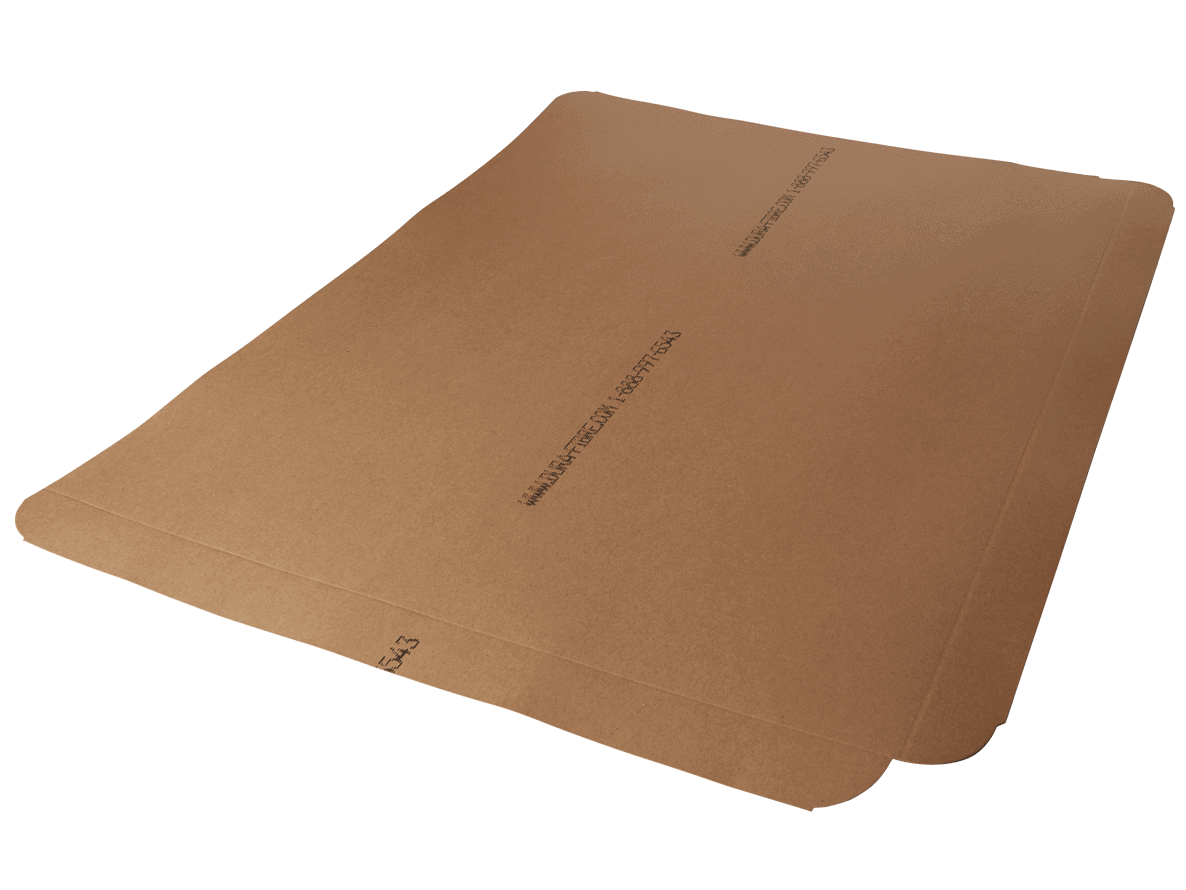
Consider a few final factors.
Forklift slip sheets do require a specialized forklift attachment. Some models operate best with a dedicated lift truck, while others are designed for easier swapping back and forth with forks. There is also the design of the pulling tabs–do you want or need to be able to pull from all four sides or just two? Having two tabs is the normal design–one in the length and one tab in the width. Also, the greater the experience of the operator the potential to use shorter tabs–which reduces the overall size of the slip sheet and thereby reduces the cost. Finally for some use cases, you may consider special requirements for coatings and/or printing.
Start realizing the savings with paperboard slip sheets.
- Less expensive than wood and plastic pallets–offering major savings
- Much lighter and allow for higher stacking–saving significant freight
- Safer–no splinters and nails–not heavy to handle by hand
- Can be designed for re-use in a closed loop system for huge savings
- Save space–reducing warehousing costs
- Save landfill space–they are recyclable–the most sustainable option
We have seen these factors combine to provide our customers with millions of dollars in savings, so don’t let concerns over initial research stop you from saving, too. Dura-Fibre offers the engineering expertise to guide you through the process. We have the widest range of options to fit your use case. Please contact us for further information.